Continuous casting process has largely replaced conventional ingot casting for the production of semifinished copper shapes like rods. The advantages of continuous casting, for example better productivity, improved quality and cost savings, are numerous. The optimisation of the process is going on all the time, as better productivity and quality are always required.
Continuous casting of copper rods, which are generally used for the production of drawn wire. It can be accomplished by different methods. Upcast process is one of the main methods in the world to produce oxygen-free copper wire rod. In this casting system, solidification occurs inside a submerged die after which the solid rod is pulled vertically upwards.
Primarily continuous casting of copper is a heat extraction process. The conversion of molten copper into a solid copper rod involves removal of superheat and latent heat of fusion. One of the most critical and essential components of the continuous casting equipment is the mould. Being the primary heat extraction device, it is required to solidify the molten copper. Heat transfer in the mould sets the limits for maximum productivity.Thus it influences the final quality of a copper product.
upcasting machine consisted of a furnace, a cooler, a withdrawal machine and a coiler. Cooler of the casting machine consists of primary (mould) and secondary cooling parts. The primary cooling consists basically of a graphite die which is partly submerged in molten metal. The upper portion of the die is surrounded by a water-cooled copper jacket which solidifies the molten metal as it passes through the die. The cooler is located above the furnace and the lower end of the cooler is submerged into the melt. The entire machine can be moved up and down according to the melt level in the furnace. So that the die is always at the same depth in the melt. This means also a constant metallostatic pressure during the casting. The rod was pulled from the die by tandem pinch rolls and was then guided to the coiler.
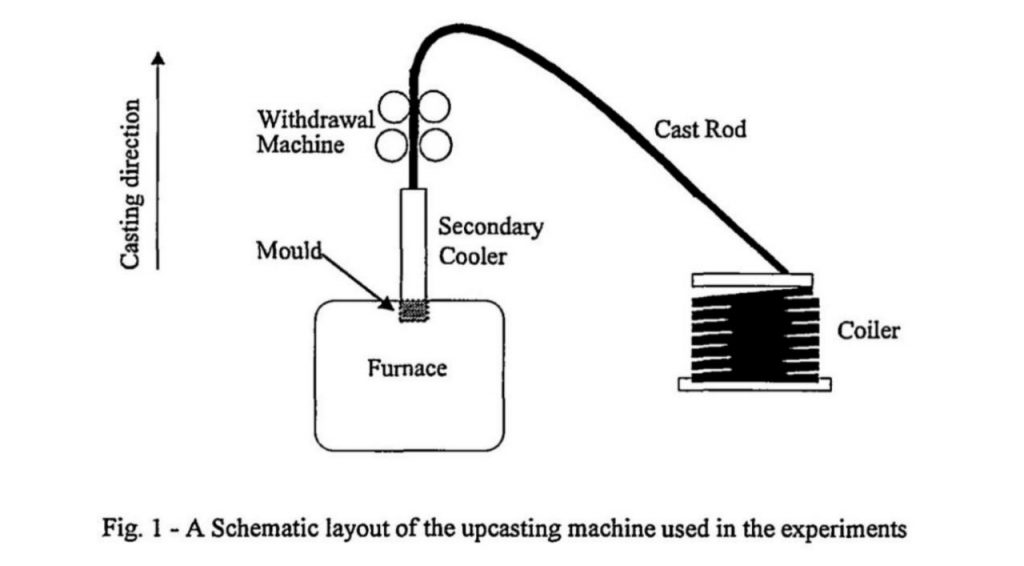
The mould of the casting machine consists of a copper mould, a graphite die, an insulation cup, a protective cup and water channels.
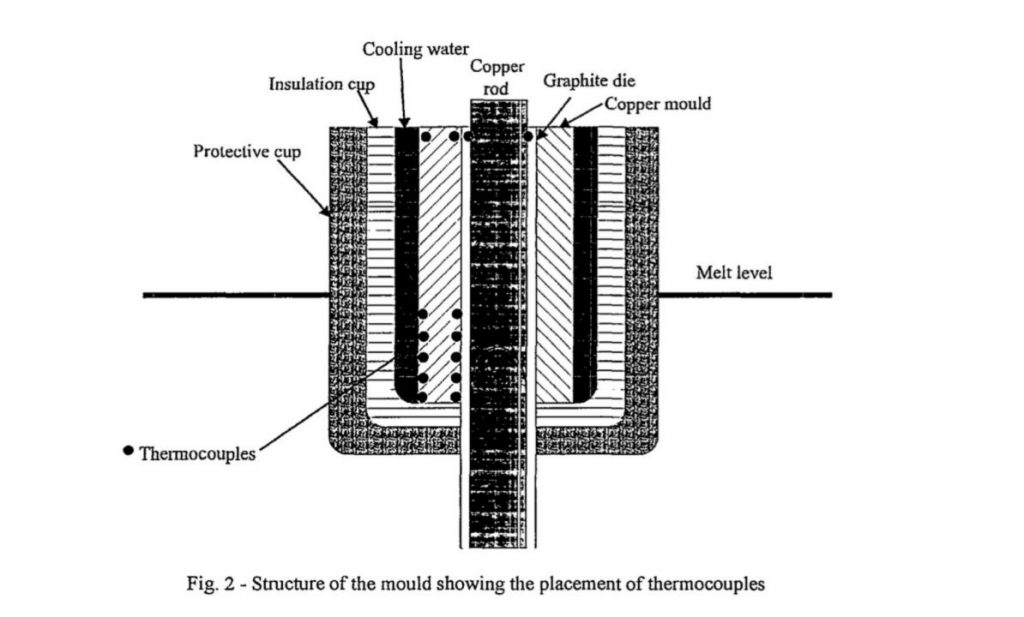
HEAT TRANSFER PROCEDURE
Efficient extraction of heat from the liquid/solid ingot within the mould is crucial to the success of the continuous casting process. In order to control the casting we have to know the heat transfer procedure phenomena happening in the mould. The heat flow is rather complicated because it is controlled primarily by the formation of an air gap which separates the mould from the cast copper rod. The location and size of the gap are influenced simultaneously by shrinkage of the shell and metallostatic pressure exerted by the liquid pool.
First there is contact of the liquid metal with mould before a solid skin is fonmed due to the solidification of the melt. After that solidification shrinkage occurs and an air gap is formed between the copper rod and the mould. The air gap constitutes the largest single heat flow resistance and its evolution depends mainly on the solidification shrinkage of the cast rod. Heat from the rod surface is transferred to the mould cooling water after the air gap formation via a series of thermal resistances, as shown in the schematical presentation in Fig. 3:
(1)conduction and radiation across an air gap separating the graphite die and the solidified copper rod
(2) conduction through the graphite die wall
(3) conduction and (radiation) across the interface between the graphite die and the copper mould
(4) conduction through the copper mould wall
(5) convection at the copper mould/cooling water interface.
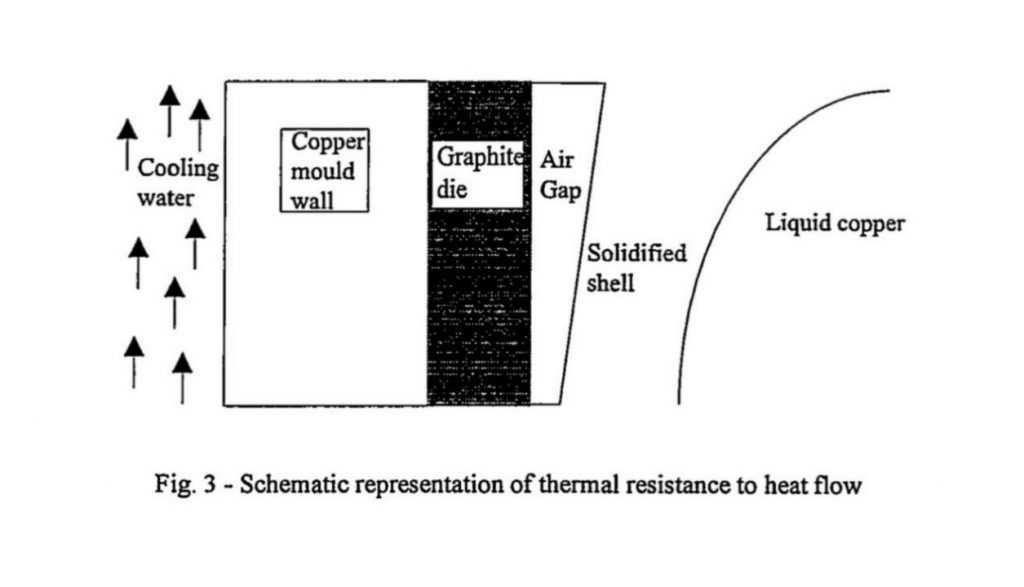